La fabrication de l’acier de la torche olympique des Jeux de Paris 2024, a d’ailleurs fait office de défi pour les équipes de l’usine Arcelormittal à Florange, plus habituées à la grande industrie qu’aux petites séries de quasi-orfèvrerie.
Ça y est, la flamme olympique est allumée. À 100 jours du début des Jeux de Paris 2024, la vasque accueillant la flamme a été embrasée mardi sur le site antique d’Olympie, en Grèce. De là, elle va ensuite rejoindre Athènes où elle embarquera à bord du Belem avec une arrivée prévue sur le territoire français, à Marseille, le 8 mai. Débutera alors un tour de France, en métropole et dans les outremers, avant l’allumage de la flamme à Paris pour la cérémonie d’ouverture des Jeux le 26 juillet.
Un voyage hautement symbolique, et très scruté, qui met en lumière un savoir-faire entièrement français puisque la torche olympique qui transporte la flamme a été conçue par le designer Mathieu Lehanneur et fabriquée en Moselle, dans l’usine sidérurgique Arcelormittal de Florange, site emblématique de la lutte pour le maintien de l’industrie en France.
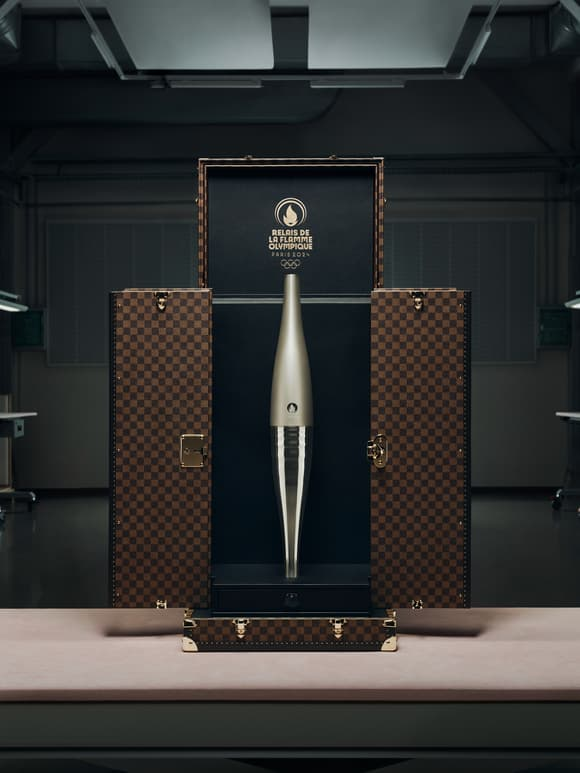
Un défi technique
La fabrication de l’acier de la torche olympique des Jeux de Paris 2024, a d’ailleurs fait office de défi pour des équipes plus habituées à la grande industrie -de l’automobile ou du bâtiment- qu’aux petites séries de quasi-orfèvrerie.
Une seule bobine d’acier enroulé sorti du laminoir a ainsi suffi pour fabriquer les 2.000 torches nécessaires aux relayeurs de la flamme des Jeux olympiques et paralympiques de Paris 2024 cet été. En six ou sept passages sous les rouleaux et les jets d’eau, la barre de métal en fusion de 25 cm d’épaisseur s’aplatit et s’allonge en un long et fin ruban d’acier. Un panache de fumée blanche envahit le sombre laminoir.
« On s’est préparé comme des sportifs, il fallait répondre à beaucoup de questions techniques nouvelles », explique à l’AFP Mourad Sedki, ingénieur qualité à Florange.
« On n’a pas le choix, c’est pour le climat qu’on l’a fait aussi », ajoute Aurélie Lemière, ingénieure également à Florange, qui a été sélectionnée pour être porteuse de la flamme sur une des étapes du relais en Moselle.
Une torche modèle de sobriété énergétique
De quels défis parlent-ils? Quel est le rapport entre les Jeux olympiques, la flamme, un groupe sidérurgiste sponsor de l’opération, et l’évolution des températures mondiales?
« La première difficulté, c’était la confidentialité. Rien ne devait fuiter, les équipes ne devaient pas être au courant, pour ne pas ébruiter l’affaire trop tôt, elles ont appris plus tard qu’un brame (barre, poutre) d’acier recyclé, laminé à Florange, avait servi à fabriquer les torches », dit Franck Wasilewski, chef de projet.
« Pas de tableau de bord, rien dans l’ordinateur, on a tout préparé en équipe resserrée », ajoute-t-il. Mais ce sont quand même des ingénieurs de quatre centres de recherche différents du groupe qui se sont alliés pour concevoir, réaliser, tester et valider la qualité de l’acier utilisé, précise Jean-Luc Thirion, directeur général de la recherche du groupe.
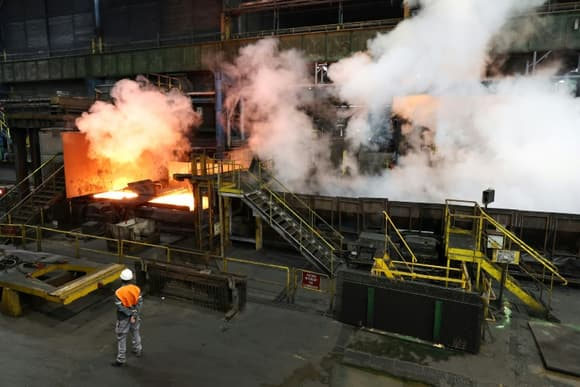
Pour des Jeux qui revendiquent la sobriété, la torche oblongue de 70 cm de haut est en acier recyclé. Ce qui fait baisser considérablement son bilan carbone. L’acier issu du recyclage de ferrailles en four électrique émet environ 0,5 tonne de CO2 par tonne produite, contre 1,8 tonne pour celui qui sort d’un haut fourneau, en raison de la combustion du charbon utilisé pour désoxyder le minerai de fer qui se transforme en fonte d’acier.
La torche est aussi rechargeable et réutilisable par une dizaine de porteurs différents. À la différence des Jeux précédents, où près de 12.000 torches avaient été fabriquées, six fois plus que pour Paris 2024. « Il a fallu être très innovant pour arriver à une torche de 0,7 mm d’épaisseur, avec une mise en forme compliquée », et des « défis techniques d’assemblage », fait valoir Jean-Luc Thirion. Un peu comme faire réaliser un objet d’art dans l’industrie lourde.
« Florange est toujours là! »
ArcelorMittal a offert l’acier, mais espère maintenant en retirer un peu de gloire. Tout au moins dans le petit monde des ingénieurs et de l’industrie. Car dans l’industrie traditionnelle, l’acier recyclé reste encore souvent réservé aux poutres de construction. Bien cachées dans la structure des bâtiments, les imperfections ou les « bulles » sur le métal, dues aux restes d’autres métaux ou peintures de leur précédente vie qui se sont amalgamés dans le four de recyclage, sont invisibles à l’œil nu.
L’acier plat, neuf, sans aspérité, utilisé pour les voitures, l’électroménager, sort, lui, souvent directement des hauts fourneaux. Le défi était donc de prouver, y compris en interne, qu’une pièce de grande qualité et de grande finesse pouvait être fabriquée à partir d’acier recyclé issu de vieilles carrosseries ou machines à laver.
« Les chercheurs se sont impliqués avec beaucoup d’enthousiasme et en vraie complémentarité d’innovation avec le designer de la torche Mathieu Lehanneur », ajoute Jean-Luc Thirion.
« Et Florange est toujours là! », lance, bravache, le directeur de l’usine Jean-François Malcuit. Souvenir des rudes joutes sociales qui ont fait de Florange un symbole de la désindustrialisation en 2013, lors de la fermeture de ses derniers hauts fourneaux après vingt mois de bras de fer entre syndicats, gouvernement et direction.
Aujourd’hui, l’usine emploie environ 2.000 personnes et est tournée vers des technologies d’avenir comme la galvanisation. Les hauts fourneaux promis à la démolition devraient eux-mêmes être « entièrement recyclés » dans les futurs fours électriques prévus à Dunkerque. « C’est le cycle naturel de la vie de l’acier », dit Jean-François Malcuit. Mais onze ans après, le chantier de démolition n’a toujours pas commencé.
CL avec AFP